Practical Contamination Control
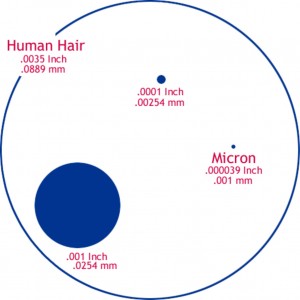
To prevent system contamination, filtration is required. This is the size of one micron, which dictates ISO standards depending on the system and it’s component parts.
Ron Durante, Price On-Site
You have heard it before: the biggest issue associated with hydraulic system failure is contamination. Over and over again it is stated, and our field service technicians confirm, that 75 to 80 percent of hydraulic problems are related to contamination. Our techs are considered hero’s simply by going out on a service call, pulling out a cartridge valve, cleaning it with brake cleaner and compressed air and reinstalling it. When in fact, 90 percent of the systems we work on don’t meet the ISO cleanliness target set forth by the manufacturer for the system’s most sensitive component. If your system operates intermittently, the prime mover operates at RPMs less than 1800 and pressures are less than 2500 PSI, you probably are not experiencing contamination related issues with your hydraulic system. But, if you’re running at higher RPMs, higher pressures, have multiple shifts and the company, along with customers, depend on this piece of equipment to be in service then do what it takes to hit your cleanliness target. Once you hit the your cleanliness target and maintain operation at this level, you can expect the system components to last three times longer. The clean, cool oil will last five times longer and you will experience a significant drop in machine downtime.
Simply put, you need to particle count to get a baseline of current contamination levels. All team members should be involved and educated so they understand the importance of correct filtration and fluid handling, training can be the most important step in the process. Help maintenance technicians understand correct fluid handling procedures and what an ISO code of 16/14/12 means. However, most of all, realize that any maintenance, no matter how careful, will introduce contamination.
Once you have a particle count baseline, you need to install the correct filters and breathers, seal up the system and most likely install a recirculation loop. After twenty-four hours, particle count again to confirm the cleanliness target is achieved. If done correctly, you will beat and never rise above the target which allows you to perform maintenance events. Remember, each time your ISO code goes up, the level of contaminates doubles. Miss it by two codes and your oil is four times as dirty. If you beat it by a code, you halved the amount of contaminates being introduced to components. Your success or failure can be measures by particle counts in an oil sample. The overall goal in a practical contamination control plan is to keep the system clean to the point that contamination is no longer a factor in component failure.
Practical contamination control is one of the least expensive way to improve the life of your hydraulic system. The associated costs are always less than equipment downtime and repairs. With contamination the causes are obvious, the solutions available, the benefits great and the return on investment is almost immediate.
More from my site
Comments are closed.
-
Archives
- August 2022
- April 2022
- August 2021
- December 2020
- August 2020
- January 2019
- September 2018
- March 2018
- February 2018
- December 2017
- November 2017
- October 2017
- September 2017
- May 2017
- April 2017
- March 2017
- February 2017
- October 2016
- September 2016
- August 2016
- July 2016
- June 2016
- March 2016
- September 2013
- July 2013
- March 2013
- January 2013
- December 2012
- November 2012
- October 2012
- September 2012
- August 2012
- July 2012
- June 2012
- May 2012
- April 2012
- March 2012
- February 2012
Signup Today
to get our monthly Enews delivered to your inbox.